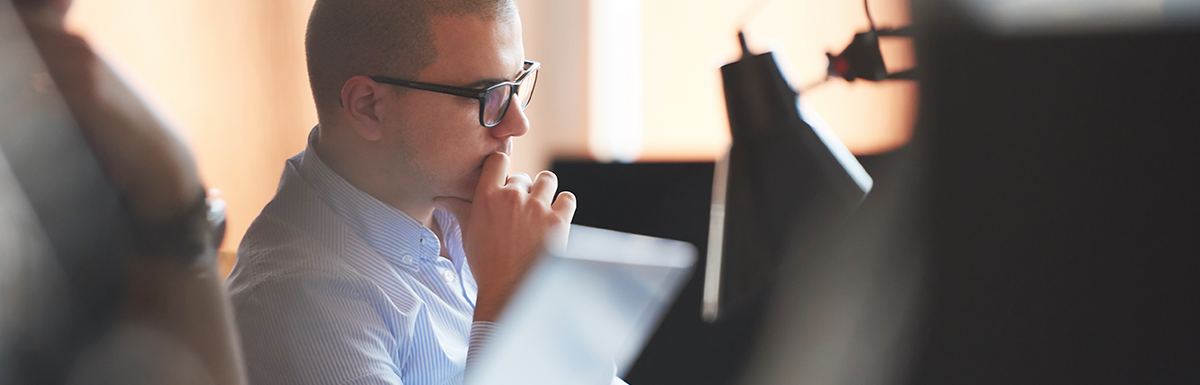
Since using staffing in manufacturing is a common practice that is often an expensive one, costing companies hundreds of thousands of dollars in staffing fees, companies need to measure the cost per hire and really take a deep dive in retention rates for staffing and other sources of hire.
Increasing numbers of manufacturers are starting to use predictive analytics algorithms. It helps with every aspect of the manufacturing process, such as efficiency in sourcing and hiring, workforce productivity, or performance forecasts. Technology is the catalyst behind manufacturing’s ongoing transformation. Cloud technology, in particular, is proving essential for manufacturers seeking to eliminate old barriers and seize new and emerging opportunities. To put it simply, predictive analytics algorithms are using available data to predict and to improve manufacturing operations and processes which makes recruiting and hiring metrics an important part of your upcoming hiring strategy.
Staffing agencies working on placements in the manufacturing sector and industry must take these analytics into consideration, so a deeper dive into turnover and retention rates by manager and shift schedule are important metrics to analyze. Higher turnover by shift might lead to the team considering to increase or create a shift differential pay.
The Top Five Manufacturing Recruiting and Hiring Metrics to Measure
When it comes to the best recruiting metrics for the basics, quantity metrics are a good place to start. A deeper dive leads us into quality metrics, and the most helpful analyses include a balance of both. Quantity metrics include time to fill, candidate to hire ratio, and for staffing agencies, placement ratio. Quality metrics are, obviously, quality of hire – but also numbers like job order to placement ratio when you’re measuring recruiter efficiency. Here’s a rundown of the top five metrics to consider when recruiting for manufacturing.
Cost per hire
Cost per hire is the average amount of money you spent on making a hire. This metric is useful when you are creating or tracking your recruiting budget and providing reports to client companies. Their budget is top of mind, and it should be on yours as well.
Benchmarking data is important to this metric. Bersin by Deloitte estimates the national average cost per hire, regardless of talent acquisition maturity, is $4,000. But for the manufacturing industry, that number is $5,611 for manufacturing jobs.
Candidate-to-hire ratio
Candidate-to-hire ratio can vary from the number of applications to hires, to the applicant-to-interview ratios for initial interviews as well as final interviews. Note that yield ratios in recruitment and selection are often useless as lone percentages. Companies need a continuous process of analyzing data and comparing HR metrics across time in order to draw better conclusions. This is essential in predictive hiring analytics.
Source of hire
Source of hire calculates which applicant sources are performing the best across the board, by position and among recruiters. This helps you measure internal performance by your recruiting team as well as which source is returning the best applicants.
Tracking source of hire (SoH) will help you distribute your hiring resources to the most effective recruiting channels. Calculate this metric by dividing your recruiting source yield by number of applicants from the recruiting source. Use this metric to determine which sources, job boards or websites are most effective for hiring for your business.
Related: How to Use Recruitment Marketing to Reach Manufacturing Candidates
Quality of hire
Quality of hire measures which source of hire produces the best-performing candidates or those with the longest tenure. This can be a difficult metric because it measures the value new hires bring to a company and “value” can be defined in multiple ways. Value usually means how much a new hire contributes to their company’s long term success by completing tasks, improving their work and helping others, but in manufacturing there are other indicators to take into consideration, such as shift work, productivity, skills gap, and performance rankings.
It can be helpful here to measure beyond the number of new hires. Consider how many fully productive employees you have added and how many days from hire it takes before your new hire is a fully productive employee. It’s also helpful to measure hiring manager success by establishing benchmarks to determine each hiring manager’s “new hire churn,” so they can share best practices for onboarding and the ramp-up process.
First time send out to placement ratio (FTSP)
First time send out to placement ratio (FTSP), also called the Sendouts Per Hire ratio, is going to be a key metric for any staffing agency making placements in the manufacturing industry. This boils down to the number of candidates referred to your manufacturing client versus the total number hired by your client.
You can send a lot of promising candidates to your clients, but that doesn’t matter unless they get hired. This is a perfect illustration of comparing quantity metrics to quality metrics. One hundred sendouts in a month is a great quantity metric. Making zero placements as a result of those 100 sendouts is a terrible quality metric.
Finally, with unemployment at 17-year lows, finding qualified talent is among manufacturers’ top priorities. As in other critical performance areas, comparing how your recruiting funnel measures up to others in your industry can reveal performance gaps that you need to close. This is why recruitment and hiring metrics are essential to help you establish a baseline and determine what works most cost effectively in your manufacturing hiring efforts.